Применение карбонитрации при изготовлении энергетической арматуры
С.Г. Цих, В.И. Гришин, В.Н. Лисицкий, Ю.А. Глебова, ОАО НПО «ЦНИИТМАШ», МГТУ им. Н.Э. Баумана, г. Москва
На машиностроительных предприятиях России, производящих паровые турбины и запорную арматуру для тепловых и атомных станций, для повышения надежности и долговечности деталей широко используется низкотемпературная технология их поверхностного упрочнения – газовое азотирование. Для большинства деталей применение технологии азотирования имеет целью повышение поверхностной твердости, износостойкости и коррозионной стойкости в паровой, воздушной и масляных средах.
Азотированию подвергаются несколько сотен наименований деталей паровых турбин. Это детали многочисленных узлов регулирования и парораспределения, различного назначения клапаны, втулки, буксы, золотники; штоки, шпиндели, тарелки и другие детали запорной арматуры, к которым предъявляются требования обеспечения хорошей плотности и отсутствия утечек воды или пара. Для этого посадочные места должны иметь высокую твердость и длительно сохранять свои первоначальные размеры до температуры 540 °С. Азотирование применяется и для упрочнения резьбовых соединений с целью предотвращения заедания при высокой температуре, а также как антикоррозионная защита углеродистых сталей. Примеры применения азотирования в турбостроении приведены в таблице
Стали для азотирования деталей турбин и их назначение
Марка стали | Назначение стали | Цель азотирования | Толщина слоя, мм | Твердость по ТУ, HV |
1 | 2 | 3 | 4 | 5 |
38х2МЮА | втулки, валики, кулачки и др. детали, работающие при нормальной температуре | Повышение износостойкости и усталостной прочности | 0,20-0,50 | 500-900 |
18х2Н4вА | Шестерни, вал-шестерни, валы, шлицевые валы и др | Повышение износостойкости и усталостной прочности | 0,20-0,30 | 500-650 |
25х2МФ (ЭИ 10) 20х1М1Ф1Тр (ЭП 182) | Штоки, втулки, клапаны, буксы, болты, гайки | Повышение износостойкости при температу- ре до 500 °с и для устранения схватывания | 0,20-0,50 | 500-800 |
35хМА | То же | То же, но для температуры 400-450 °с | 0,20-0,40 | 450-600 |
20х3МвФ (ЭИ 415) | То же | То же, но для температуры 500-535 °с | 0,15-0,20 | 500-800 |
25х2М1Ф (ЭИ 723) | То же | То же, но для температуры до 535 °с | 0,20-0,40 | 500-700 |
1х13 | лопатки сопловых аппаратов | для увеличения эрозионной стойкости в паровой среде | 0,10-0,20 | 450-700 |
15х11МФ 15х12вМФ | лопатки сопловых аппаратов, штоки, буксы, втулки, клапаны | для увеличения эрозионной стойкости, износостойкости и устранения схватывания при температуре 535-565 °с | 0,10-0,20 0,10-0,20 | 450-800 450-700 |
40х | Болты, шпильки, гайки, валики | для устранения схватывания и повышения коррозионной стойкости | 0,15-0,20 | 400-500 |
50хФА 60с2 | винтовые пружины и др. детали | для повышения коррозионной стойкости в паровой и влажной среде | 0,10-0,20 0,10-0,20 | 550-750 400-600 |
Углеродистые стали 20, 30, 35, 40, 45 | серьги, поршни, скобы, колесо импеллера, рабочие колеса насосов и др. детали | для повышения коррозионной стойкости в паровой, влажной и масляной среде | до 0,65 | Контролю твердости не подвергаются |
Существенным недостатком технологии газового азотирования является большая длительность технологического цикла, достигающая нескольких десятков часов, и повышенная хрупкость азотированного слоя.
Среди процессов, направленных на интенсификацию скорости насыщения сталей азотом, особое место занимает технология азотирования в жидких средах, при которой происходит преимущественное насыщение сталей азотом и углеродом. Жидкостное азотирование в расплавах солей обеспечивает высокую скорость нагрева, уменьшает термические напряжения и коробление изделий, позволяет регулировать в широких пределах скорость охлаждения после насыщения и т.п.
История низкотемпературного процесса жидкостного азотирования берет начало с 30-х годов прошлого столетия, когда Д.А. Прокошкин [1,2] сообщил о технических возможностях жидкостного цианирования, его простоте и высокой эффективности. Впервые было отмечено, что поверхностное упрочнение при низкотемпературном процессе связано не с формированием мартенситных структур, как в случае высокотемпературного цианирования, а с образованием нитридов и карбонитридов, и сам процесс протекает в условиях, исключающих превращение, как это имеет место при других видах поверхностного упрочнения (цементация, нитроцементация, высокотемпературное цианирование, поверхностная закалка). Поэтому локальные разогревы в месте контакта при трении, контактном нагружении не приводят к местному разупрочнению азотированных и карбонитрированных слоев, чего нельзя избежать в случае мартенситных структур, получаемых при закалке. Это объясняет и предельно малые величины деформации и коробления деталей при низкотемпературном насыщении деталей азотом (газовое азотирование) и азотом и углеродом (жидкостное азотирование, карбонитрация).
Широкое освоение технологии низкотемпературного цианирования сдерживалось использованием в составе расплава высокотоксичных цианидов. В 50-х годах ХХ в. фирма «Дегусса» (Германия) предложила состав ванны, содержащий наряду с цианидами 50% цианатов щелочных металлов и тем самым положила начало знаменитому «Тенифер»-процессу – «мягкому азотированию». По сравнению с цианированием «ядовитость» процесса сократилась вдвое, и он был внедрен на более чем 1000 машиностроительных предприятиях многих стран.
Учитывая высокую эффективность технологии жидкостного азотирования в плане существенного повышения эксплуатационных свойств деталей, технологичность, экономичность и простоту процесса, в дальнейшем развитие технологии было направлено на поиск состава расплава на неядовитой основе.
В результате исследования химизма процесса низкотемпературного цианирования было установлено, что реакции в расплаве идут путем окисления:
2 KCN + O2 = 2 KCNO
2 KCNO + O2 = K2CO3 + 2 N + CO
2 CO = CO2 + C
c выделением атомов азота и углерода в результате окисления цианата. Не сам цианид калия (KCN), а продукт его окисления – цианат калия (KCNO) – является поставщиком активных атомов азота и углерода в рабочем расплаве. В отличие от цианида цианат калия – вещество неядовитое, пожаро- и взрывобезопасное, хорошо растворимое в воде. Именно цианаты представляют интерес и являются наиболее подходящими веществами для осуществления жидкостных процессов химико-термической обработки.
Задача, связанная с разработкой технологически приемлемой жидкой среды для низкотемпературного упрочнения металлических изделий, в середине 70-х годов была решена в МГТУ им. Н.Э. Баумана проф. Прокошки- ным Д.А. [3]. Им предложена и получила промышленное внедрение экологически безвредная технология, которую автор назвал «карбонитрация». Расплав на основе цианата калия (KCNO – 75-85%) и поташа (K2CO3 – 15-25%) обладает высокой химической активностью, хорошей технологичностью, имеет низкую температуру плавления и при рабочих температурах процесса 550-580 °С характеризуется высокой жидкотекучестью.
Среди технологий низкотемпературного упрочнения карбонитрация в расплавах солей является наиболее экономичным процессом, т.к. сокращает длительность выдержки до 0,5-6 ч, вместо 10-60 ч при газовом азотировании. При этом практически отсутствует хрупкость карбонитрированного слоя, характерная для длительных процессов газового азотирования.
Впоследствии, на основе собственных разработок, подобные технологии появились в Германии (новый Тенифер-процесс TF 1), в США («Мелонайт»), в Японии («Мягкое азотирование»), во Франции («Сюрсульф») и др., где заложен тот главный принцип, который впервые был реализован в методе карбонитрации.
Сущность метода карбонитрации заключается в том, что детали машин из конструкционных, нержавеющих, теплостойких инструментальных и быстрорежущих сталей подвергают нагреву в расплаве солей при 540-600 °С с выдержками 5-40 мин для режущего инструмента и 1-6 ч для деталей машин и штампового инструмента в зависимости от требуемой толщины упрочненного слоя. Процесс карбонитрации прост в осуществлении, не требует сложного оборудования. Стоимость обработки в зависимости от размера деталей и компоновки садки не превышает 2-8% стоимости детали.
Применение карбонитрации для обработки деталей повышает усталостную прочность на 50-80%, резко увеличивает износостойкость по сравнению с цементацией, нитроцементацией, газовым азотированием, обеспечивает минимальные величины деформаций и микронную точность деталей. Технология применима для упрочнения деталей из любых марок сталей и чугуна. Процесс карбонитрации позволяет обеспечить: высокую скорость нагрева, равномерность температуры в объеме ванны, в широких пределах регулировать скорость охлаждения и, как правило, является окончательной операцией технологического цикла изготовления деталей. Карбонитрация деталей, изготавливаемых из конструкционных сталей, обеспечивает получение высоких значений поверхностной твердости и сопротивления износу и может применяться без последующей механической обработки.
Рис.1. Структура стали 09Г2С после карбонитрации, 570 °C, 2 ч
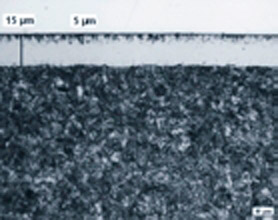
После карбонитрации углеродистых и низколегированных сталей перлитного класса на поверхности деталей образуется упрочненный слой, состоящий из двух зон (рис. 1). Верхняя зона толщиной до 15 мкм по данным рентгеноструктурного анализа представляет собой карбонитрид типа Fe (N,C) или оксикарбонитрид типа 3 Fe (N,C,О) в зависимости от состава стали. Под карбонитридным слоем располагается диффузионная зона (гетерофазный слой), состоящая из твердого раствора углерода и азота в железе с включениями карбонитридных фаз, твердость которой значительно выше твердости сердцевины и плавно снижается от поверхности к основе. В таблице ниже приведены характеристики карбонитрированного слоя. С увеличением легирования конструкционных сталей существенно возрастает поверхностная твёрдость, толщина упрочненного слоя при этом уменьшается.
Режимы обработки и характеристики карбонитрированного слоя углеродистых и низколегированных сталей
Марка стали | Твердость, Н100 | Общая толщина слоя, мкм | Толщина карбонитридного слоя, мкм | |||||||
сердцевина | поверхность | Время карбонитрации, ч | Время карбонитрации, ч | |||||||
1 | 2 | 4 | 6 | 1 | 2 | 4 | 6 | |||
20 | 170 | 400-500 | 220 | 300 | - | - | 5 | 9 | 14 | - |
45 | 190 | 400-500 | 190 | 250 | - | - | 5 | 8 | 13 | - |
60 | 210 | 500-600 | 170 | 220 | - | - | 3 | 6 | 10 | - |
У8 | 220 | 600-700 | - | - | - | - | 2 | 5 | 8 | - |
У10 | 240 | 700-750 | - | - | - | - | - | - | - | - |
40Х | 220 | 550-700 | 190 | 270 | 380 | 460 | 10 | 14 | 20 | 25 |
30ХГСА | 220 | 700-900 | 180 | 260 | 360 | 450 | 9 | 13 | 17 | 20 |
40Х1НВА | 260 | 700-900 | 160 | 240 | 340 | 410 | 8 | 12 | 15 | 18 |
38Х2МЮА | 280 | 800-1200 | 150 | 220 | 320 | 360 | 8 | 12 | 15 | 18 |
18ХГТ | 200 | 700-800 | 180 | 260 | 360 | 440 | 12 | 15 | 19 | 22 |
18Х2Н4ВА | 250 | 700-900 | 160 | 220 | 310 | 390 | 9 | 13 | 16 | 19 |
На рис. 2 и 3 представлены результаты исследования распределения микротвердости по толщине слоя различных конструкционных сталей. С увеличением содержания в сталях нитридо- и карбидообразующих элементов (Cr, Mo, V) общий уровень твердости слоя повышается. Это связано с образованием мелкодисперсных карбонитридов легирующих элементов, плотность распределения которых в твердом растворе углерода и азота в железе уменьшается от поверхности к сердцевине.
Рис. 2. Распределение твердости по толщине слоя сталей 10 (1), 20 (2), 09Г2С (3) после карбонитрации по режимам: 1 – 590 °С, 3 ч, 2 – 570 °С, 2,25 ч, 3 – 570 ° С, 3 ч
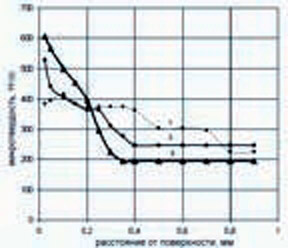
Рис. 3. Распределение твердости по толщине слоя сталей 40Х (1), 40ХН (2), 40ХМФА (3), 30ХГСА (4). Карбонитрация 570 °С, 5 ч
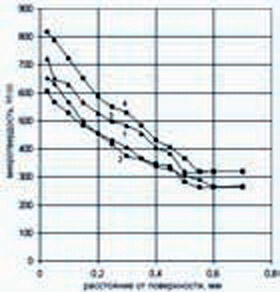
К материалам ряда деталей паровых и гидравлических турбин предъявляются требования высокой коррозионной стойкости в сочетании с износостойкостью.
Так, детали узлов регулирования паровых турбин, работающие при температуре до 565 °С, должны обладать достаточной сопротивляемостью коррозионному и эрозионному воздействию пара, а также удовлетворительной износостойкостью в условиях сухого трения при взаимном перемещении. Детали сервомоторов, работающие в среде конденсата при температуре 70-80 °С, должны иметь высокую коррозионную стойкость и удовлетворительную работоспособность в условиях сухого трения или водяной смазки. Для поверхностного упрочнения этих деталей на заводах применяется технология газового азотирования. Но, как показано ниже, азотированный слой обладает в два раза меньшей стойкостью к износу по сравнению с карбонитрированным.
Испытания карбонитрированного слоя на износостойкость показывают наличие трех стадий. Первая стадия связана с приработкой и износом пористой верхней части карбонитрированного слоя (рис. 1, верхняя часть слоя толщиной 5 мкм) и занимает небольшое место в износе. Вторая характеризуется исключительно низкой скоростью износа карбонитридной фазы. Слой изнашивается без выкрашивания и сколов, что свидетельствует о его высокой пластичности и вязкости. Третья фаза относится к износу гетерофазного слоя. Здесь в массе феррита присутствуют дисперсные карбиды и нитриды железа и легирующих элементов, и такая структура вообще характеризуется высоким сопротивлением износу.
Сравнительные испытания на износостойкость различных видов диффузионных покрытий показывают, например: скорость износа стали 20 после цементации более, чем в 20 раз выше, чем после карбонитрации (см. таблицу) (рис. 4).
Износостойкость стали 20Х после цементации и карбонитрации
Метод химико- термической обработки | Толщина упрочненного слоя, мкм | Условия испытаний | Скорость износа, мг/км пути трения | |
Нагрузка, Н | Скорость скольжения, м/с | |||
Цементация | 800 | 500 | 0,5 | 0,15/180 |
800 | 1000 | 1,5 | ||
Карбонитрация | ||||
Карбонитридный слой | 14 | 500 | 0,5 | 0,007/5,5 |
14 | 1000 | 1,5 | ||
Гетерофазный слой | 270 | 500 | 0,5 | 0,025/150 |
270 | 1000 | 1,5 | ||
Примечание. Указана скорость износа при трении со смазкой (числитель) и без смазки (знаменатель) |
Рис. 4. Зависимость износа стали 20 от пути трения со смазкой. 1 – карбонитрированный слой, 2 – гетерофазный слой, 3 – цементированный слой
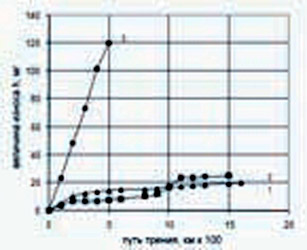
Рис. 5. Сравнительные испытания на свинчивание бурильных замков ЗЛ–152 с фосфатированием и карбонитрацией резьбы. 2 и 6 – фосфатирование, 3 и 5 – карбонитрация 570 °С, 2,5 ч (3) и 5 ч (5)
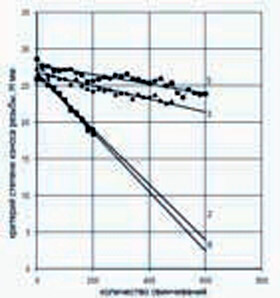
А в сравнении с фосфатированием, используемым в качестве противозадирного покрытия резьбовых соединений, карбонитрация резьбовых соединений из стали 40ХН в 4 раза снижает скорость износа резьбы (рис. 5).
Даже газовое азотирование, являющееся одним из близких аналогов процесса карбонитрации, показывает износостойкость более чем в 2 раза меньшую, чем при карбонитрации (рис. 6).
Рис. 6. Износостойкость рычага рулевого управления снегохода из стали 10 после карбонитрации (1) и серийного режима газового азотирования (2)
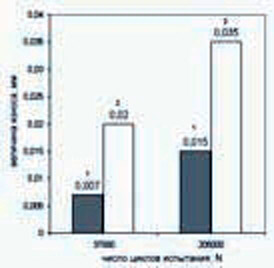
Рис. 7. Распределение твердости по толщине слоя нержавеющих сталей 20Х13 (1), 14Х17Н2 (2), 12Х18Н10Т (3). Карбонитрация 590 °С, 6 ч
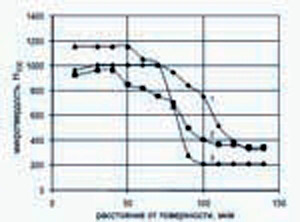
Надежность и долговечность деталей из нержавеющих хромистых и аустенитных сталей, работающих в различных условиях эксплуатации, зависят не только от свойств основного металла, но и от состояния сравнительно тонких поверхностных слоев. В энергомашиностроении для повышения поверхностной твердости, износостойкости, задиростойкости, эрозионной стойкости, усталостной прочности этого класса конструкционных сталей применяют газовое азотирование. Но этот процесс, во-первых, слишком длительный, во-вторых, наблюдается деформация и коробление деталей, в-третьих, – фаза, образующаяся на поверхности при насыщении нержавеющих сталей азотом, оказывается очень хрупкой и её приходится удалять операцией шлифования. Сам технологический процесс газового азотирования усложняется, так как приходится вводить в муфель депассиватор, устраняющий окисную пленку с поверхности нержавеющих сталей.
Процесс жидкостной карбонитрации нержавеющих сталей лишен указанных недостатков. Скорость насыщения в расплаве солей выше, чем в газовых средах, а одновременное насыщение азотом и углеродом позволяет получать на поверхности стальных изделий карбонитридный слой высокой твердости (рис. 7) и практически лишенный хрупкости, в отличие от чисто нитридного. В результате отпадает необходимость последующей механической обработки, и, кроме того, карбонитридный слой существенно повышает износостойкость и снижает коэффициент трения поверхностных слоев контактирующих деталей до 5 раз. Это подтверждают сравнительные исследования значений коэффициента трения стали 10Х18Н10Т после закалки, газового азотирования и карбонитрации (рис. 8).
Рис. 8. Изменение коэффициента трения стали 12Х18Н10Т в зависимости от удельного давления при контактном трении. 1 – закалка 1150 °С, 2 – азотирование 620 °С, 35 ч, 3 – карбонитрация 570 °С, 12 ч
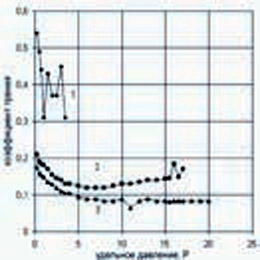
Рис. 9. Распределение твердости по толщине наплавленного слоя стали 25Х1МФ после карбонитрации 570 °С, 3 ч
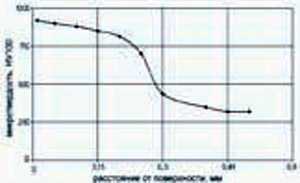
Необходимо отметить, что нами разработана технология ремонта шпинделей из стали 25Х1МФ, подвергнутых газовому азотированию. Технология включает в себя следующие операции:
- Обдирка азотированного слоя на глубину 0,5-0,7 мм.
- Наплавка (аргонодуговая или лазерная).
- Мехобработка.
- Полировка
- Карбонитрация
В результате на поверхности формируется упрочненный слой с высокой твердостью, низким коэффициентом трения (рис. 9).
На ряде фирм карбонитрации подвергаются детали запорной арматуры общего назначения и на высокие параметры температуры и давления энергетического, газо- и нефтедобывающего оборудования (штоки, шпиндели, золотники, в том числе с зубчатым приводом, тарелки, шиберы, оси, втулки, специальной конструкции гайки с обычной и трапециидальной резьбой, пробки шаровых кранов и др.). Технология карбонитрации корпусов вентилей DN 10-50 из сталей 20, 09Г2С, 25Х1М1Ф, помимо существенного повышения эксплуатационных свойств, хорошо зарекомендовала себя и как способ антикоррозионной защиты, что позволило исключить операцию окраски. На рис. 10 представлены примеры деталей, подвергаемые карбонитрации.
Рис. 10.1. Корпус, шпиндель, грундбукса. Сталь 20, 35, 09Г2С, 25Х1М1Ф, 38Х2МЮА, 14Х17Н2.
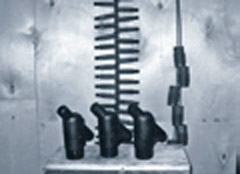
Рис. 10.2. Клапан. Сталь 25Х1М1ФТЮР (l = 1300 мм)
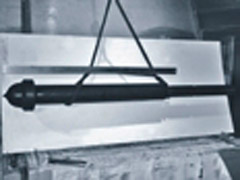
Рис. 10.3. Пробка. Сталь 08Х18Н10Т
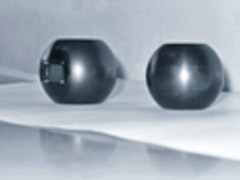
Рис. 10.4. Золотник, рейка, шпиндель. Сталь 14Х17Н2, 12Х1810Т
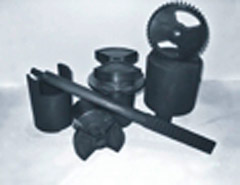
Рис. 10.5. Шпиндель. Сталь 25Х1М1Ф, 25Х2М1Ф (длина до 1500 мм)
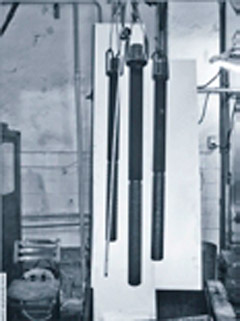
Рис. 11. Технологическая линия жидкостной карбонитрации
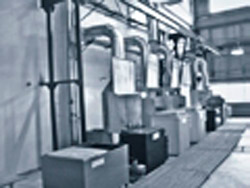
Для реализации технологии жидкостной карбонитрации разработано и изготавливается оборудование, составляющее технологическую линию жидкостной карбонитрации (ТЛЖК) и позволяющее проводить упрочнение деталей длиной до 1300 мм и диаметром до 600 мм. В состав ТЛЖК в промышленном варианте входят: печь подогрева деталей, печь-ванна карбонитрации, ванны промывки, обезжиривания, оксидирования, охлаждения, накопительная ёмкость для промстока и испаритель промстоков. На рис. 11 показана одна из таких линий [6,7].
В совершенствовании технологии жидкостной карбонитрации представляет интерес так называемый НОК-процесс (низкотемпературное оксикарбонитрирование), разработанный российскими исследователями [9]. Позже аналогичный процесс, предложенный фирмой «ДЕГУССА» (Германия), получил название TUFFTRYDE – QPQ. Эта технология, первоначально задуманная для улучшения товарного вида деталей, резко понижает коэффициент трения и, по данным немецких исследователей [10], существенно повышает коррозионную стойкость деталей из сталей перлитного и мартенситного классов. При испытании в солевом тумане, в растворе соли с перекисью водорода коррозионная стойкость деталей, обработанных по технологии QPQ, превосходит стойкость гальванического хромового покрытия.
Себестоимость обработки деталей по технологии QPQ на 40% меньше стоимости технологии нанесения гальванического покрытия.
НОК-процесс включает в себя следующую последовательность операций: карбонитрация → охлаждение и выдержка в нитритно-щелочном расплаве ванны оксидировния при 350-400 °С → охлаждение на воздухе → промывка → полировка → повторное оксидирование в расплаве → промывка.
Низкий коэффициент трения и высокая коррозионная стойкость сталей с оксикарбонитридным покрытием по технологии НОК после проверки эксплуатационных свойств дают основания рассматривать данную технологию в качестве процесса для поверхностного упрочнения деталей из низколегированных сталей перлитного класса и хромистых нержавеющих сталей и, в частности, как замена технологии гальванического хромирования, например, для пробок шаровых кранов из стали 09Г2С и ряда других изделий энергомашиностроения и других отраслей промышленности.
В заключение следует отметить, что технология жидкостной карбонитрации в настоящее время нами внедрена и широко используется при изготовлении различных деталей на таких предприятиях как: «Чеховский завод энергетического машиностроения», «Чеховский завод «Машиностроитель», «Корпорация Сплав» г. Великий Новгород, «Тяжпромарматура» г. Алексин, «Фирма Союз-01» г. Москва, «Севермаш» г. Рыбинск, «Уренгойгазпром», «Сургутнефтегаз», «Нефтегазгеофизика» г. Тверь, «Станкоагрегат» г. Москва, «Газмаш» г. Чайковский, г. Балакирево и др.
Список литературы
- Прокошкин Д.А. Химические и термические методы обработки стали. М.-л.: оНтп, 1938.
- Прокошкин Д.Аа. теория и практика цианирования быстрорежущих сталей. М.: ВНиитоМ, 1940.
- Прокошкин Д.А. а.с. 576350 ссср, Мки3 с22с27/0 опубл. в Б. и., №3, 1977.
- Прокошкин Д.А. Химико-термическая обработка металлов – карбонитрация. М.: Машиностроение, Металлургия, 1984, 240 с.
- Супов А.В. создание процесса карбонитрации. сборник научных трудов: «Металловедение. термическая и химико-термическая обработка сплавов». М.: МГту им. Н.Э. Баумана, 2003.
- Цих C.Г., Щеглов М.T., Гришин В.B., Лисицкий В.Н. разработка технологических процессов для карбонитрации крупногабаритных деталей. сборник научных трудов: «Металловедение. термическая и химико-термическая обработка сплавов». М.: МГту им. Н.Э. Баумана, 2003.
- Цих С.Г., Пласконь И.А., Гришин В.И., Лисицкий В.Н. разработка технологической линии жидкостной карбонитрации и процессов упрочнения запасных частей к основному оборудованию и инструменту. Материалы научно-технической конференции «обеспечение эффективного функционирования уренгойского нефтегазодобывающего комплекса», г. анапа,2003 г.- М.: ооо «ирЦ Газпром», 2004.
- Цих С.Г., Щеглов М.Е., Гришин В.И., Лисицкий В.Н., Мурадов А.В. исследование закономерностей комбинированного упрочнения структуры поверхностного слоя стали 25Х1МФ. НтЖ «Защита окружающей среды в нефтегазовом комплексе», 2002, №3, с. 14-17.
- Прокошкин Д.А., Супов А.В., Богомолов А.М., Кошенков В.Н. карбонитрация режущего инструмента в соляных ваннах. МитоМ. № 4, 1981.
- Г. Валь. Влияние режимов нитроцементации и последующего окисления на свойства деталей. МитоМ. № 7, 1991.