Застосування карбонітраціі при виготовленні енергетичноі арматури
С.Г. Цих, В.И. Гришин, В.Н. Лисицький, Ю.А. Глєбова, ОАО НПО «ЦНИИТМАШ», МГТУ ім. Н.Е. Баумана, м. Москва
На машинобудівних підприємствах Росії, які виробляють парові турбіни і запірну арматуру для теплових і атомних станцій, для підвищення надійності та довговічності деталей широко використовується низькотемпературна технологія їх поверхневого зміцнення - газове азотування. Для більшості деталей застосування технології азотування має на меті підвищення поверхневої твердості, зносостійкості і корозійної стійкості в паровому, повітряному і масляному середовищах.
Азотуванню піддаються кілька сотень найменувань деталей парових турбін. Це деталі численних вузлів регулювання і паророзподілу, різного призначення клапани, втулки, букси, золотники; штоки, шпинделі, тарілки та інші деталі запірної арматури, до яких пред'являються вимоги забезпечення надійної щільності і відсутності витоків води або пари. Для цього посадочні місця повинні мати високу твердість і довго зберігати свої початкові розміри до температури 540 ° С. Азотування застосовується і для зміцнення різьбових з'єднань з метою запобігання заїдання при високій температурі, а також як антикорозійний захист вуглецевих сталей. Приклади застосування азотування в турбінобудуванні наведені в таблиці
Сталі для азотування деталей турбін та іх призначення
Марка сталі | Призначення сталі | Мета азотування | Товщина шару, мм | Твердість по ТУ, HV |
1 | 2 | 3 | 4 | 5 |
38х2МЮА | втулки, валики, кулачки та ін. деталі, що працюють при нормальній температурі | Підвищення зносостійкості та утомної міцності | 0,20-0,50 | 500-900 |
18х2Н4вА | Шестерні, вал-шестерні, вали, шліцьові вали та ін | Підвищення зносостійкості та утомної міцності | 0,20-0,30 | 500-650 |
25х2МФ (ЭИ 10) 20х1М1Ф1Тр (ЭП 182) | Штоки, втулки, клапани, букси, болти, гайки | Підвищення зносостійкості при температурі до 500 ° С і для усунення схоплювання | 0,20-0,50 | 500-800 |
35хМА | Те саме | Те саме, але для температури 400-450 °с | 0,20-0,40 | 450-600 |
20х3МвФ (ЭИ 415) | Те саме | Те саме, але для температури 500-535 °с | 0,15-0,20 | 500-800 |
25х2М1Ф (ЭИ 723) | Те саме | Те саме, але для температури до 535 °с | 0,20-0,40 | 500-700 |
1х13 | лопатки соплових апаратів | для збільшення ерозійної стійкості в паровому середовищі | 0,10-0,20 | 450-700 |
15х11МФ 15х12вМФ | лопатки соплових апаратів, штоки, букси, втулки, клапани | для збільшення ерозійної стійкості, зносостійкості і усунення схоплювання при температурі 535-565 °с | 0,10-0,20 0,10-0,20 | 450-800 450-700 |
40х | Болти, шпильки, гайки, валики | для усунення схоплювання і підвищення корозійної стійкості | 0,15-0,20 | 400-500 |
50хФА 60с2 | гвинтові пружини та ін. деталі | для підвищення корозійної стійкості в паровому і вологому середовищі | 0,10-0,20 0,10-0,20 | 550-750 400-600 |
Вуглецеві сталі 20, 30, 35, 40, 45 | сережки, поршні, скоби, колесо импеллера, робочі колеса насосів та ін. деталі | для підвищення корозійної стійкості в паровому, вологому і масляному середовищі | до 0,65 | Контролю твердістю не піддаються |
Істотним недоліком технології газового азотування є велика тривалість технологічного циклу, що досягає декількох десятків годин, і підвищена крихкість азотованого шару.
Серед процесів, спрямованих на інтенсифікацію швидкості насичення сталей азотом, особливе місце займає технологія азотування в рідких середовищах, при якій відбувається переважне насичення сталей азотом і вуглецем. Рідинне азотування в розплавах солей забезпечує високу швидкість нагріву, зменшує термічні напруги і викривлення виробів, дозволяє регулювати в широких межах швидкість охолодження після насичення і т.п.
Історія низькотемпературного процесу рідинного азотування бере початок з 30-х років минулого століття, коли Д.А. Прокотячий [1,2] повідомив про технічні можливості рідинного ціанування, його простоті і високій ефективності. Вперше було відзначено, що поверхневе зміцнення при низькотемпературному процесі пов'язано не з формуванням мартенситних структур, як в разі високотемпературного ціанування, а з утворенням нітриду і карбонітридів, і сам процес протікає в умовах, що виключають перетворення, як це має місце при інших видах поверхневого зміцнення (цементація, нітроцементація, високотемпературне ціанування, поверхневе гартування). Тому локальні розігріви в місці контакту при терті, контактному навантаженні не призводять до місцевого знеміцнення азотованих і карбонітрованих шарів, чого не можна уникнути в разі мартенситних структур, одержуваних при гартуванні. Це пояснює і гранично малі величини деформації і викривлення деталей при низькотемпературному насиченні деталей азотом (Газове азотування) та азотом і вуглецем (рідинне азотування, Карбонітрація).
Широке освоєння технології низькотемпературного ціанування стримувалося використанням в складі розплаву високотоксичних ціанідів. У 50-х роках ХХ ст. фірма «Дегусса» (Німеччина) запропонувала склад ванни, у якому поруч з ціанідами 50% ціанатів лужних металів і тим самим поклала початок знаменитому «Теніфер»-процесу - «м'якому азотуванню». Порівняно з ціануванням «отруйність» процесу скоротилася вдвічі, і він був впроваджений на більш ніж 1000 машинобудівних підприємствах багатьох країн.
З огляду на високу ефективність технології рідинного азотування в плані істотного підвищення експлуатаційних властивостей деталей, технологічність, економічність і простоту процесу, в подальшому розвиток технології було направлено на пошук складу розплаву на неотруйного основі.
В результаті дослідження хімізму процесу низькотемпературного ціанування було встановлено, що реакції в розплаві йдуть шляхом окислення:
2 KCN + O2 = 2 KCNO
2 KCNO + O2 = K2CO3 + 2 N + CO
2 CO = CO2 + C
з виділенням атомів азоту і вуглецю в результаті окислення ціанату. Чи не сам ціанід калію (KCN), а продукт його окиснення - ціанат калію (KCNO) - є джерелом активних атомів азоту і вуглецю в робочому розплаві. На відміну від ціаніду ціанат калію - речовина неотруйна, пожежо- та вибухобезпечна, добре розчинна у воді. Саме ціанати представляють інтерес і є найбільш підходящими речовинами для здійснення рідинних процесів хіміко-термічної обробки.
Завдання, пов'язане з розробкою технологічно прийнятною рідкого середовища для низькотемпературного зміцнення металевих виробів, в середині 70-х років було вирішене в МГТУ ім. Н.Е. Баумана проф. Прокошкіним Д.А. [3]. Ним запропонована і отримала промислове впровадження екологічно нешкідлива технологія, яку автор назвав «Карбонітрація». Розплав на основі цианата калію (KCNO - 75-85%) і поташу (K2CO3 – 15-25%) має високу хімічну активність, хорошу технологічність, з низькою температурою плавлення і при робочих температурах процесу 550-580 ° С характеризується високою рідиноплинністю.
Серед технологій низькотемпературного зміцнення Карбонітрація в розплавах солей є найбільш економічним процесом, тому що скорочує тривалість витримки до 0,5-6 год, замість 10-60 год при газовому азотуванні. При цьому практично відсутня крихкість карбонітрованого шару, характерна для тривалих процесів газового азотування.
Згодом, на основі власних розробок, подібні технології з'явилися в Німеччині (новий Теніфер-процес TF 1), в США ( «Мелонайт»), в Японії ( «М'яке азотування»), у Франції ( «Сюрсульф») та ін., де закладено той головний принцип, який вперше був реалізований в методі карбонітрації.
Суть методу карбонітрації полягає в тому, що деталі машин з конструкційних, нержавіючих, теплостійких інструментальних і швидкорізальних сталей піддають нагріванню в розплаві солей при 540-600 ° С з витягами 5-40 хв для ріжучого інструменту і 1-6 год для деталей машин і штампового інструменту в залежності від необхідної товщини зміцненого шару. Процес карбонітрації простий у виконанні, що не вимагає складного обладнання. Вартість обробки в залежності від розміру деталей і компоновки садки не перевищує 2-8% вартості деталі.
Застосування карбонітрації для обробки деталей підвищує втомну міцність на 50-80%, різко збільшує зносостійкість в порівнянні з цементацією, нітроцементацією, газовим азотуванням, забезпечує мінімальні величини деформацій і мікронну точність деталей. Технологія застосовна для зміцнення деталей будь-яких марок сталей і чавуну. Процес карбонітрації дозволяє забезпечити: високу швидкість нагріву, рівномірність температури в обсязі ванни, в широких межах регулювати швидкість охолодження і, як правило, є остаточною операцією технологічного циклу виготовлення деталей. Карбонітрація деталей, що виготовляються з конструкційних сталей, забезпечує отримання високих значень поверхневої твердості і опору зносу і може застосовуватися без подальшої механічної обробки.
Рис.1. Структура сталі 09Г2С після карбонітраціі, 570 °C, 2 год
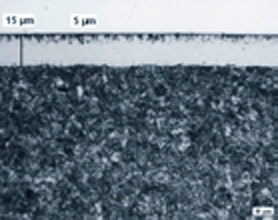
Після карбонітрації вуглецевих і низьколегованих сталей перлітного класу на поверхні деталей утворюється зміцнений шар, що складається з двох зон (рис. 1). Верхня зона товщиною до 15 мкм за даними рентгеноструктурного аналізу являє собою карбонітрид типу Fe (N, C) або оксікарбонітрід типу 3 Fe (N, C, О) в залежності від складу сталі. Під карбонітридним шаром розташовується дифузійна зона (гетерофазний шар), що складається з твердого розчину вуглецю і азоту в залізі з включеннями карбонітридних фаз, твердість якої значно вище твердості серцевини і плавно знижується від поверхні до основи. У таблиці нижче наведені характеристики карбонітрованого шару. Зі збільшенням легування конструкційних сталей істотно зростає поверхнева твердість, товщина зміцненого шару при цьому зменшується.
Режими обробки і характеристики карбонітрованого шару вуглецевих і низьколегованих сталей
Марка сталі | Твердість, Н100 | Загальна товщина шару, мкм | Товщина карбонітридного шару, мкм | |||||||
серцевина | поверхня | Час карбонітрації, год | Час карбонітраціх, год | |||||||
1 | 2 | 4 | 6 | 1 | 2 | 4 | 6 | |||
20 | 170 | 400-500 | 220 | 300 | - | - | 5 | 9 | 14 | - |
45 | 190 | 400-500 | 190 | 250 | - | - | 5 | 8 | 13 | - |
60 | 210 | 500-600 | 170 | 220 | - | - | 3 | 6 | 10 | - |
У8 | 220 | 600-700 | - | - | - | - | 2 | 5 | 8 | - |
У10 | 240 | 700-750 | - | - | - | - | - | - | - | - |
40Х | 220 | 550-700 | 190 | 270 | 380 | 460 | 10 | 14 | 20 | 25 |
30ХГСА | 220 | 700-900 | 180 | 260 | 360 | 450 | 9 | 13 | 17 | 20 |
40Х1НВА | 260 | 700-900 | 160 | 240 | 340 | 410 | 8 | 12 | 15 | 18 |
38Х2МЮА | 280 | 800-1200 | 150 | 220 | 320 | 360 | 8 | 12 | 15 | 18 |
18ХГТ | 200 | 700-800 | 180 | 260 | 360 | 440 | 12 | 15 | 19 | 22 |
18Х2Н4ВА | 250 | 700-900 | 160 | 220 | 310 | 390 | 9 | 13 | 16 | 19 |
На рис. 2 і 3 представлені результати дослідження розподілу мікротвердості по товщині шару різних конструкційних сталей. Зі збільшенням вмісту в сталях нітрідо- і карбідоутворюючих елементів (Cr, Mo, V) загальний рівень твердості шару підвищується. Це пов'язано з утворенням дрібнодисперсних карбонитридов легуючих елементів, щільність розподілу яких в твердому розчині вуглецю і азоту в залізі зменшується від поверхні до серцевини.
Рис. 2. Розподіл твердості по товщині шару сталей 10 (1), 20 (2), 09Г2С (3) після карбонітрації по режимам: 1 – 590 °С, 3 год, 2 – 570 °С, 2,25 год, 3 – 570 ° С, 3 год
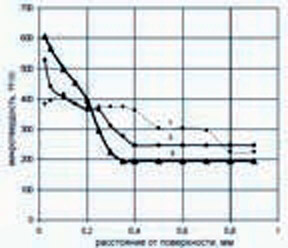
Рис. 3. Розподіл твердості по товщині шару сталей 40Х (1), 40ХН (2), 40ХМФА (3), 30ХГСА (4). Карбонітрація 570 °С, 5 год
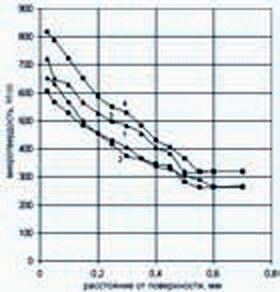
До матеріалів ряду деталей парових і гідравлічних турбін пред'являються вимоги високої корозійної стійкості в поєднанні зі зносостійкістю.
Таким чином, деталі вузлів регулювання парових турбін, що працюють при температурі до 565 ° С, повинні володіти достатньою опірністю корозійного і ерозійного впливу пари, а також задовільною зносостійкістю в умовах сухого тертя при взаємному переміщенні. Деталі сервомоторів, що працюють в середовищі конденсату при температурі 70-80 ° С, повинні мати високу корозійну стійкість і задовільну працездатність в умовах сухого тертя або водяного мастила. Для поверхневого зміцнення цих деталей на заводах застосовується технологія газового азотування. Але, як показано нижче, азотований шар має в два рази меншу стійкість до зносу в порівнянні з карбонітруваням.
Випробування карбонітрованого шару на зносостійкість показують наявність трьох стадій. Перша стадія пов'язана з приробленням і зносом пористої верхньої частини карбонітрованого шару (рис. 1, верхня частина шару завтовшки 5 мкм) і займає невелике місце у зносі. Друга характеризується виключно низькою швидкістю зносу карбонітридної фази. Шар зношується без викришування і відколів, що свідчить про його високу пластичність і в'язкість. Третя фаза відноситься до зносу гетерофазного шару. Тут в масі фериту присутні дисперсні карбіди та нітриди заліза і легуючих елементів, і така структура взагалі характеризується високим опором зносу.
Порівняльні випробування на зносостійкість різних видів дифузійних покриттів показують, наприклад: швидкість зносу сталі 20 після цементації більш ніж в 20 разів вище, ніж після карбонітрації (див. таблицю) (рис. 4).
Зносостійкість сталі 20Х після цементації і карбонітрації
Метод хіміко-термічної обробки | Товщина зміцненого шару, мкм | Умови випробувань | Швидкість зносу, мг/км шляхи тертя | |
Навантаження, Н | Швидкість ковзання, м/с | |||
Цементація | 800 | 500 | 0,5 | 0,15/180 |
800 | 1000 | 1,5 | ||
Карбонітрація | ||||
Карбонітридний шар | 14 | 500 | 0,5 | 0,007/5,5 |
14 | 1000 | 1,5 | ||
Гетерофазний шар | 270 | 500 | 0,5 | 0,025/150 |
270 | 1000 | 1,5 | ||
Примітка. Вказана швидкість зносу при терті з мастилом (чисельник) і без змащення (знаменник) |
Рис. 4. Залежність зносу сталі 20 від шляху тертя з мастилом. 1 - карбонітрований шар, 2 - гетерофазний шар, 3 - цементований шар
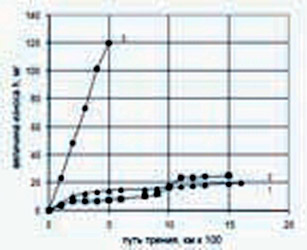
Рис. 5. Порівняльні випробування на скручування бурильних замків ЗЛ-152 з фосфатуванням і карбонітрацією нарізі. 2 і 6 – фосфатиування, 3 и 5 – карбонітрація 570 °С, 2,5 год (3) и 5 год (5)
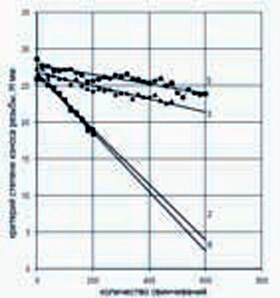
А в порівнянні з фосфатуванням, використовуваним в якості протизадирного покриття нарізних з'єднань, карбонітрація різьбових з'єднань зі сталі 40ХН в 4 рази знижує швидкість зносу нарізі (рис. 5).
Навіть газове азотування, що є одним з близьких аналогів процесу карбонітрації, показує зносостійкість більш ніж в 2 рази меншу, ніж при карбонітрації (рис. 6).
Рис. 6. Зносостійкість важеля рульового управління снігохода зі сталі 10 після карбонітрації (1) і серійного режиму газового азотування (2)
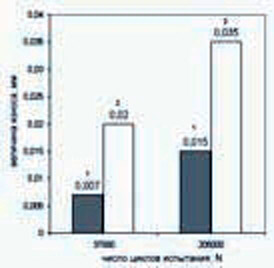
Рис. 7. Розподіл твердості по товщині шару нержавіючих сталей 20Х13 (1), 14Х17Н2 (2), 12Х18Н10Т (3). Карбонітрація 590 °С, 6 год
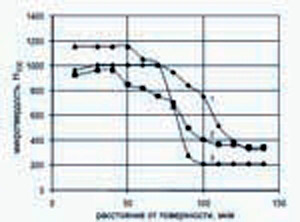
Надійність і довговічність деталей з нержавіючих хромистих і аустенітних сталей, що працюють в різних умовах експлуатації, залежать не тільки від властивостей основного металу, а й від стану порівняно тонких поверхневих шарів. У енергомашинобудуванні для підвищення поверхневої твердості, зносостійкості, задиростійкості, ерозійної стійкості, втомної міцності цього класу конструкційних сталей застосовують газове азотування. Але цей процес, по-перше, занадто тривалий, по-друге, спостерігається деформація і викривлення деталей, по-третє, - фаза, що утворюється на поверхні при насиченні нержавіючих сталей азотом, виявляється дуже крихкою і її доводиться видаляти операцією шліфування. Сам технологічний процес газового азотування ускладнюється, оскільки доводиться вводити в муфель депасиватор, що усуває окисну плівку з поверхні нержавіючих сталей.
Процес рідинної карбонітрації нержавіючих сталей позбавлений зазначених недоліків. Швидкість насичення в розплаві солей вище, ніж в газових середовищах, а одночасне насичення азотом і вуглецем дозволяє отримувати на поверхні сталевих виробів карбонітридний шар високої твердості (рис. 7) і практично позбавлений крихкості, на відміну від чисто нітрідного. В результаті відпадає необхідність подальшої механічної обробки, і, крім того, карбонітридний шар істотно підвищує зносостійкість і знижує коефіцієнт тертя поверхневих шарів контактуючих деталей до 5 разів. Це підтверджують порівняльні дослідження значень коефіцієнта тертя сталі 10Х18Н10Т після гарту, газового азотування і карбонітрації (рис. 8).
Рис. 8. Зміна коефіцієнту тертя сталі 12Х18Н10Т в залежності від питомого тиску при контактному терті. 1 – гартування 1150 °С, 2 – азотування 620 °С, 35 год, 3 – карбонітрація 570 °С, 12 год
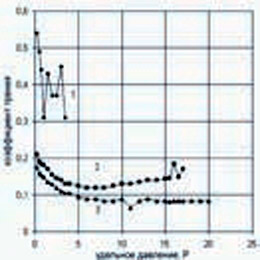
Рис. 9. Розподіл твердості по товщині наплавленого шару сталі 25Х1МФ після карбонітрації 570 °С, 3 год
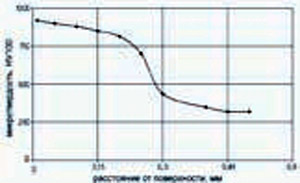
Необхідно відзначити, що нами розроблена технологія ремонту шпинделів зі сталі 25Х1МФ, підданих газовому азотуванню. Технологія включає в себе наступні операції:
- Обдирання азотированного шару на глибину 0,5-0,7 мм.
- Наплавлення (аргонодугова або лазерна).
- Мехобробка.
- Полірування
- Карбонітрація
В результаті на поверхні формується зміцнений шар з високою твердістю, низьким коефіцієнтом тертя (рис. 9).
На ряді фірм карбонітрації підлягають деталі запірної арматури загального призначення і на високі параметри температури і тиску енергетичного, газо- і нафтовидобувного обладнання (штоки, шпинделі, золотники, в тому числі з зубчастим приводом, тарілки, шибери, осі, втулки, спеціальної конструкції гайки з звичайної і трапеціїдальною наріззю, пробки кульових кранів та ін.). Технологія карбонітрації корпусів вентилів DN 10-50 зі сталей 20, 09Г2С, 25Х1М1Ф, крім істотного підвищення експлуатаційних властивостей, добре зарекомендувала себе і як спосіб антикорозійного захисту, що дозволило виключити операцію забарвлення. На рис. 10 представлені приклади деталей, що піддаються карбонітрації.
Рис. 10.1. Корпус, шпиндель, грундбукса. Сталь 20, 35, 09Г2С, 25Х1М1Ф, 38Х2МЮА, 14Х17Н2.
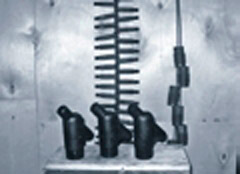
Рис. 10.2. Клапан. Сталь 25Х1М1ФТЮР (l = 1300 мм)
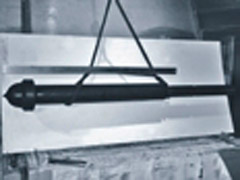
Рис. 10.3. Пробка. Сталь 08Х18Н10Т
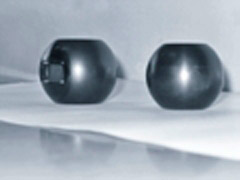
Рис. 10.4. Золотник, рейка, шпиндель. Сталь 14Х17Н2, 12Х1810Т
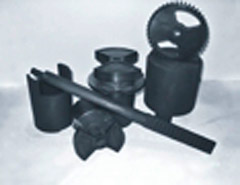
Рис. 10.5. Шпиндель. Сталь 25Х1М1Ф, 25Х2М1Ф (довжина до 1500 мм)
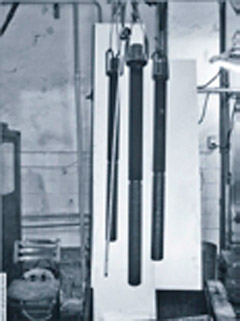
Рис. 11. Технологічна лінія рідинної карбонітрації
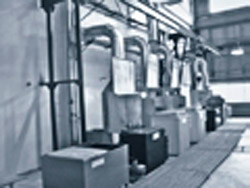
Для реалізації технології рідинної карбонітрації розроблено і виготовляється обладнання, що становить технологічну лінію рідинної карбонітрації (ТЛЖК) і дозволяє проводити зміцнення деталей довжиною до 1300 мм і діаметром до 600 мм. До складу ТЛЖК в промисловому варіанті входять: піч підігріву деталей, піч-ванна карбонітрації, ванни промивки, знежирення, оксидування, охолодження, накопичувальна ємність для промислових стоків і випарник промстоків. На рис. 11 показана одна з таких ліній [6,7].
У вдосконаленні технології рідинної карбонітрації становить інтерес так званий НОК-процес (низькотемпературне оксікарбонітрування), розроблений російськими дослідниками [9]. Пізніше аналогічний процес, запропонований фірмою «ДЕГУССА» (Німеччина), отримав назву TUFFTRYDE - QPQ. Ця технологія, спочатку задумана для поліпшення товарного виду деталей, різко знижує коефіцієнт тертя і, за даними німецьких дослідників [10], істотно підвищує корозійну стійкість деталей зі сталей перлітного і мартенситного класів. При випробуванні в сольовому тумані, в розчині солі з перекисом водню корозійна стійкість деталей, оброблених за технологією QPQ, перевершує стійкість гальванічного хромового покриття.
Собівартість обробки деталей за технологією QPQ на 40% менше вартості технології нанесення гальванічного покриття.
НОК-процес включає в себе наступну послідовність операцій: Карбонітрація → охолодження і витримка в нітритно-лужному розплаві ванни оксідування при 350-400 °С → охолодження на повітрі → промивка →полірування → повторне оксидування в розплаві → промивка.
Низький коефіцієнт тертя і висока корозійна стійкість сталей з оксікарбонітрідним покриттям за технологією НОК після перевірки експлуатаційних властивостей дають підстави розглядати дану технологію в якості процесу для поверхневого зміцнення деталей з низьколегованих сталей перлітного класу і хромистих нержавіючих сталей і, зокрема, як заміна технології гальванічного хромування, наприклад, для пробок кульових кранів зі сталі 09Г2С і ряду інших виробів енергомашинобудування і інших галузей промисловості.
В завершення слід зазначити, що технологія рідинної карбонітрації в даний час нами впроваджена і широко використовується при виготовленні різних деталей на таких підприємствах як: «Чеховський завод енергетичного машинобудування», «Чеховский завод «Машиностроітєль», «Корпорація Сплав» м. Великий Новгород, «Тяжпромарматура» м. Алєксін, «Фірма Союз-01» м. Москва, «Сєвєрмаш» г. Рибінск, «Уренгойгазпром», «Сургутнєфтєгаз», «Нєфтєгазгєофізіка» м. Тверь, «Станкоагрегат» м. Москва, «Газмаш» м. Чайковський, м. Балакірєво та ін.
Список літератури
- Прокошкін Д.А. Хімічні та термічні методи обробки сталі. М.-л.: оНтп, 1938.
- Прокошкін Д.А. Теорія і практика ціанування швидкорізальних сталей. М.: ВНиитоМ, 1940.
- Прокошкін Д.А. а.с. 576350 ссср, Мки3 с22с27/0 опубл. в Б. и., №3, 1977.
- Прокошкін Д.А. Хіміко-термічна обробка металів - карбонітрація. М.: Машинобудування, Металургія, 1984, 240 с.
- Супов А.В. Створення процесу карбонітрації. Збірник наукових праць: «Металознавство. термічна і хіміко-термічна обробка сплавів». М.: МГту ім. Н.Е. Баумана, 2003.
- Цих C.Г., Щєглов М.T., Грішин В.B., Лисицький В.Н. Розробка технологічних процесів для карбонітрації великогабаритних деталей. Збірка наукових праць: «Металознавство. Термічна і хіміко-термічна обробка сплавів». М.: МГту ім. Н.Е. Баумана, 2003.
- Цих С.Г., Пласконь И.А., Грішин В.И., Лисицький В.Н. Розробка технологічної лінії рідинної карбонітрації і процесів зміцнення запасних частин до основного обладнання та інструменту. Матеріали науково-технічної конференції «забезпечення ефективного функціонування Уренгойського нафтогазовидобувного комплексу», м. Анапа,2003 р.- М.: ТОВ «ирЦ Газпром», 2004.
- Цих С.Г., Щєглов М.Е., Грішин В.И., Лисицький В.Н., Мурадов А.В. Дослідження закономірностей комбінованого зміцнення структури поверхневого шару сталі 25Х1МФ. НТЖ «Захист навколишнього середовища в нафтогазовому комплексі», 2002, №3, с. 14-17.
- Прокошкін Д.А., Супов А.В., Богомолов А.М., Кошенков В.Н. Карбонітрація ріжучого інструменту в соляних ваннах. МитоМ. № 4, 1981.
- Г. Валь. Вплив режимів нітроцементації і подальшого окислення на властивості деталей. МитоМ. № 7, 1991.